Client: MODEC
Process: Sulphate Removal
Country: Buzios Field - Offshore Brasil
Contact Description: Seawater Treatment Process Module
Contract Date: October 2019
Contract Completion Date: January 2021
SRU Capacity: 280,200 BPD (44,540 m3/day)
Sea Water Conversion: 75%
Sea Water Feed Quality:
- TDS: 35,200 mg/l (TDS)
- Sulphate: 2,800 mg/l
Product Water Output Quality: Sulphate <50 mg/l
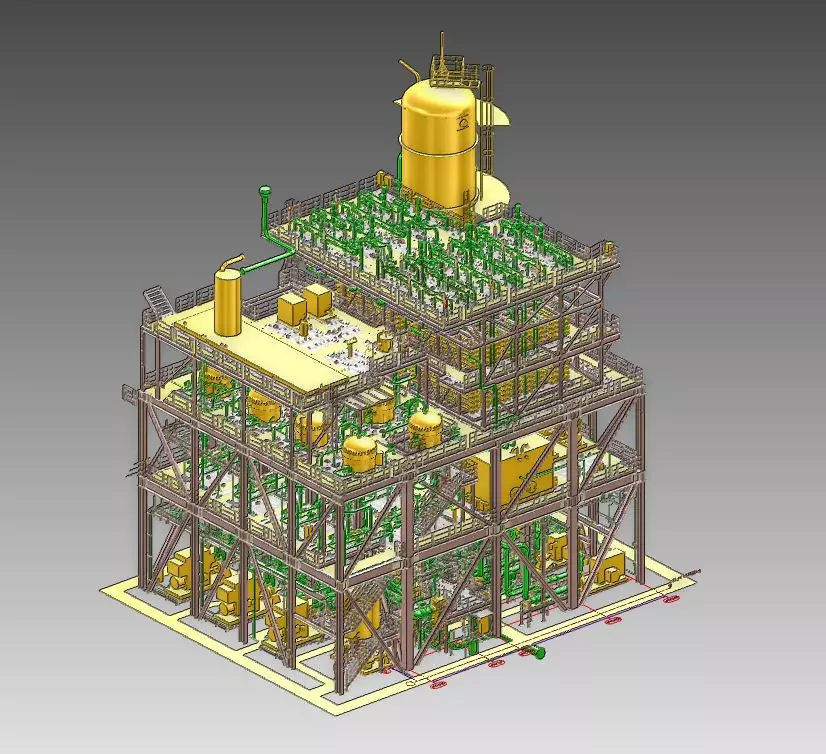
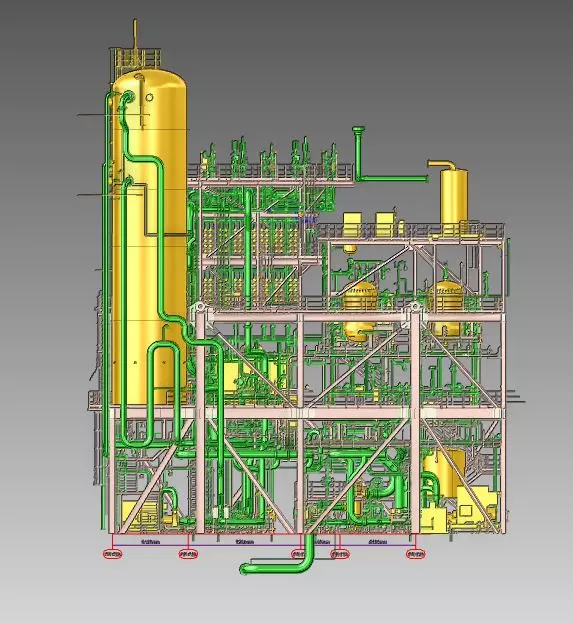
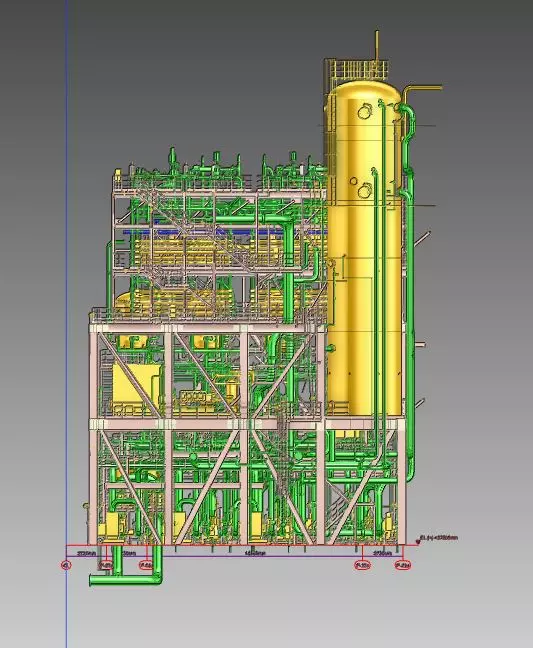
Project Description:
The project is for the design and equipment procurement of a seawater treatment process module, with construction of the Sulphate Removal membrane rack, and the provision of technical support for the main module construction, for a seawater treatment plant sized for 280,200 BPD (44,450 m3/day) of low sulphate injection water for the Almirante Barroso FPSO, that will operate in the Buzios Field, offshore Brasil.
Project Scope:
The project scope consists of a single process module comprising Coarse Strainers, UltraMEV (ultrafiltration pre-treatment), Sulphate Removal Feed Pumps, Sulphate Removal Membrane Trains, Membrane CIP system, Vacuum Deaerator Package, Water Injection Booster Pumps, Plant Control System, Piping, Valves and Instrumentation
Process Description:
Seawater is pumped using the Seawater Lift Pumps (provided by others) and directed to the seawater treatment system. The raw seawater is chlorinated via the electrochlorination package (by others) and introduced into the seawater lift pump suction lines. Sodium hypochlorite is used to limit the potential of biological activity in the downstream processes. It will also be dosed into the UF trains during Chemically Enhanced Backwash.
Automatic backwashable seawater coarse strainers remove larger particulate matter from the feed stream to the SRU plant. The filtered seawater from seawater coarse strainers is used as source water for the water injection system.
The feed stream is directed to UF pre-treatment. The UF Membrane System treats the SRU feed water to remove the majority of particles. The process uses Dow hollow fibre membrane technology in ‘dead-end’ filtration mode without the need for continuous cross flow velocity. The filtrate quality is typically expected to have an SDI < 3.
The UF filtrate is routed to Reverse Osmosis package (secondary source) or to the suction of the Sulphate Removal Unit Feed Pumps to boost the conditioned water to the required feed pressure for the membranes. The SR Feed Pumps operate in parallel. Antiscalant is dosed downstream of the Sulphate Removal Feed Pumps, decreasing the scaling tendency by limiting the formation of sparingly soluble salts in the membrane system. SBS is also dosed into common discharge piping of the Sulphate Removal Feed Pumps to remove the residual chlorine present in the seawater to prevent irreparable damage to the SR90 membranes. Finally a non-oxidizing proprietary biocide for treating the SR90 membranes is also periodically batch dosed into the same location.
The seawater flows to parallel operated Sulphate Removal Units. To achieve the specified sulphate level both stages will be fitted with Dow Filmtec type SR90-440i membranes.
The feed pressure to each SRU is controlled based on the permeate flow set point. The SRU produces 75% of the feed flow as low sulphate permeate Seawater. The low sulphate SW from each SRU is merged and then directed to the deaerator. The remaining 25% of the feed flow ends up as high sulphate content reject seawater and is directed overboard.
SRU trains are provided with automatic full and partial bypass that may be used during SRP membrane cleaning.
The treated seawater then enters the Vacuum Deaerator to remove dissolved oxygen from the water. Oxygen scavenger is dosed to the sump of the deaerator to chemically reduce the remaining oxygen further to the required levels.
Deaerated, low sulphate injection water from the deaerator is routed to water injection booster pumps. These pumps are provided to boost the feed pressure to the required pressure at the package boundary. The Deaerator tower is provided with manual bypass and additional dosing point for Oxygen Scavenger in case the Deaerator operates in bypass mode. Biocide (DBNPA) dosing points are also provided upstream and downstream of the Deaerator and can be batch dosed for sanitation purposes . Additionally Biocide (THPS) dosing point is provided upstream of the Deaerator Tower. This can only be used when the RO system (by others) is not fed from the Deaerator.
There is a membrane cleaning in Place (CIP) system for the SR and UF trains. The CIP Tanks capacity is designed for the 1st stage of SR membranes or 1 train of UF membranes wash (if applicable). CIP Pumps and cartridge filter are designed for cleaning of 1st stage of 1 SRP train (maximum capacity). One CIP Heater is provided for each CIP tank and is sized to heat up cleaning solution volume within 2 hours. Each CIP tank volume is sufficient to wash 1 membrane train (largest consumption - UF or SRP).
Chemically Enhanced Backwash (CEB) system comprises of CEB tank and pumps and allows to reuse the hypochlorite used for UF CEB clean and minimise the usage of this chemical as well as facilitates its neutralisation before disposing to overboard.