Client: MODEC Offshore Production Systems
Process: Sulphate Removal
Country: Santos Basin - Offshore Brazil
Contract Description: Seawater Treatment System - Modules MV-23
Contract Date: March 2010
Contract Completion Date: September 2011
Capacity: 150,972 BPD (24,000 m3/day)
Sea Water Conversion: 75%
Sea Water Feed Quality: 35,177 mg/l (TDS)
Product Water Output Quality: <100 mg/l sulphate
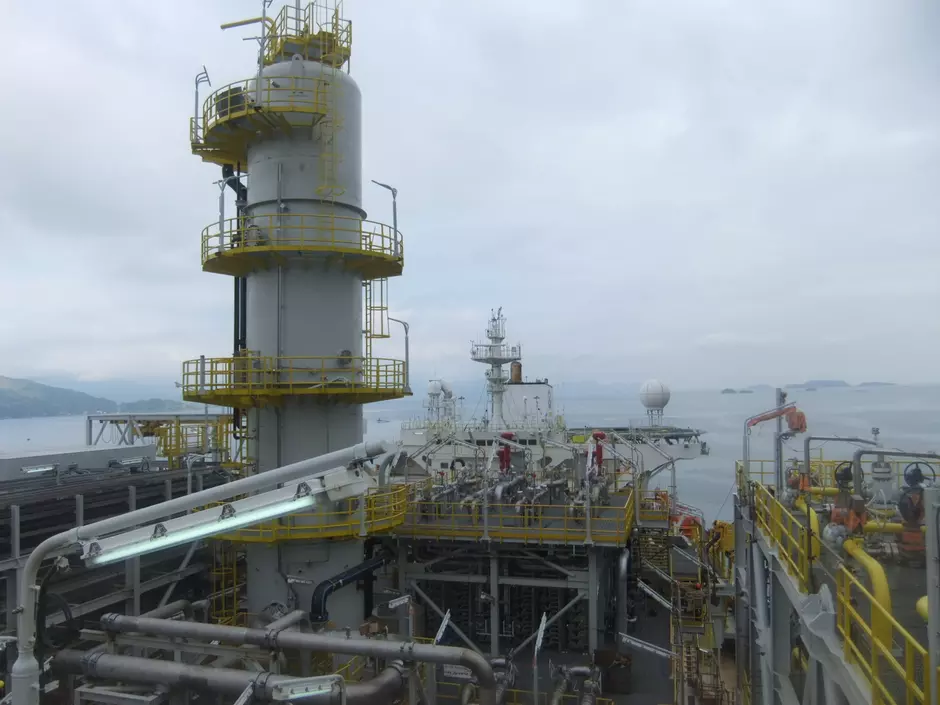
Project Description:
The project is for the design, supply of a water injection plant sized for 150,972 BPD (24,000 m3/day) of low sulphate water for the Cidade de São Paulo (Tupi 2) FPSO, which will operate in the Santos Basin, offshore Brazil.
Project Scope:
The project scope consists of a Seawater Treatment Plant in a single lift module arrangement comprising: Electro-Chlorination Unit, Seawater Coarse Strainers, Multi Media Fine Filtration, Upstream Vacuum Deaerator Package, HP Feed Pumps, Guard Cartridge Filters, Sulphate Removal Membrane System, Clean In Place System, Piping, Valves and Instrumentation.
Process Description:
Coarse filtration is provided by a set of automatic backwashable coarse strainers rated at 80µm.An electro-chlorination unit provides hypochlorite for disinfection of the water injection system. Fine filtration is then achieved by a set of multi media fine filters, complete with air scour, followed by a set of guard cartridge filters to provide fine filtration down to 10µm prior to the membrane trains. The set of fine filters supplies feed water for two (2) SRP trains.
The conditioned water is routed to a vacuum deaerator package then forwarded to the sulphate removal trains. Each membrane train is fitted with pressure vessels containing SR90-440i nanofiltration elements.A recovery of 75% is achieved by a 2:1 brine staged configuration. Brine reject from the process is discharged overboard, while the low sulphate permeate is forwarded onwards to the water injection pumps (provided by others) for injection to the wells at the required pressure. A dedicated clean in place (CIP) package, consisting of cleaning tank, heater, pump and cartridge filter vessel is provided for membrane cleaning purposes.