Client: Aibel Singapore
Process: Water Treatment System Module
Country: Australia
End User: Woodside
Contract Description: Water Treatment System
Contract Start Date: July 2016
Contract Completion Date: August 2018
SRU Capacity: 80,000 BPD (12,720 m3/day)
Sea Water Conversion: 75%
Sea Water Feed Quality:
- TDS: 34,181 mg/l
- Sulphate: 2,624 mg/l
Product Water Output Quality: Sulphate <100 mg/l
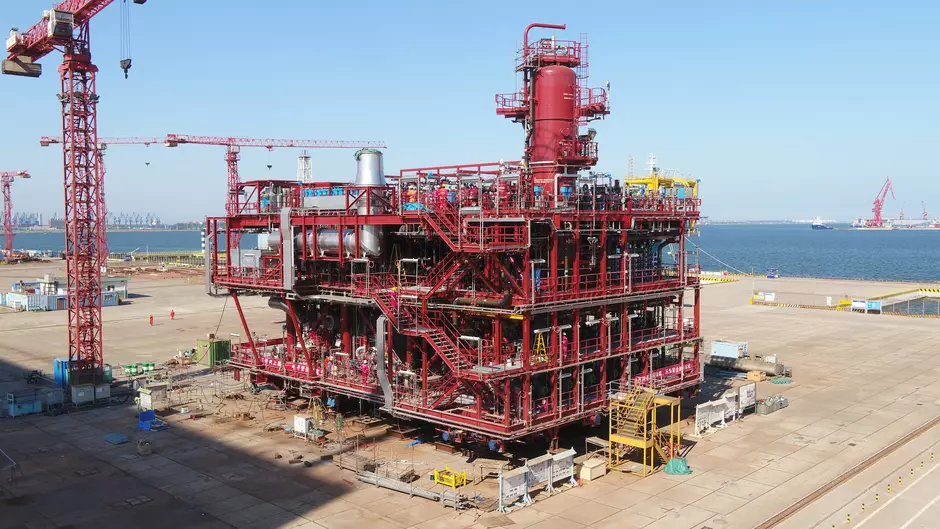
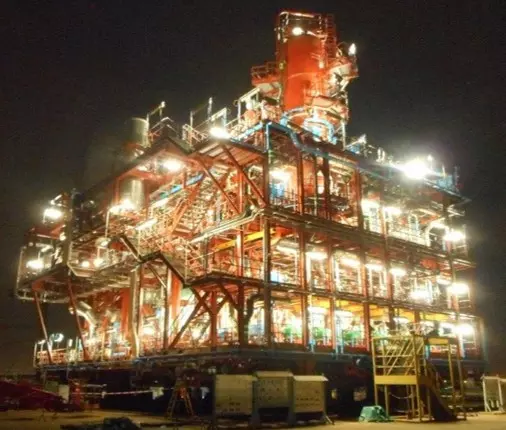
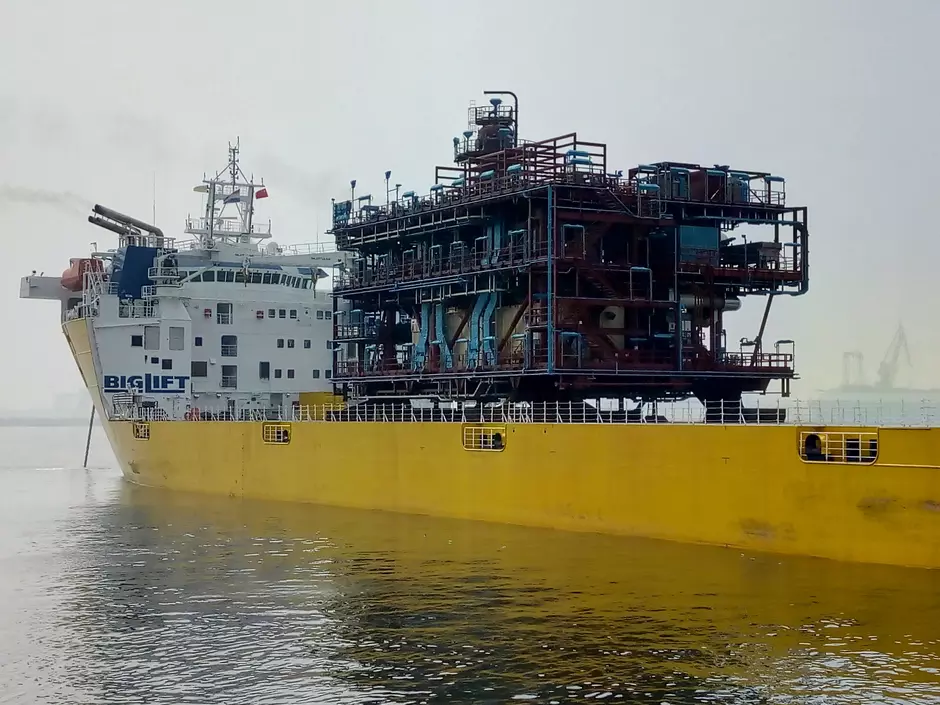
Project Description:
The project was for the design, equipment procurement and supply, and construction as a single lift integrated process module, incorporating: Coarse Filtration, Ultrafiltration (UF) Pre-treatment, Sulphate Removal membrane Process (SRP), Vacuum Deaeration, Dual Fuel Turbine driven Water Injection Pump, Electrical Switchgear and Transformers, and Plant Control Room. The system water injection capacity is 12,720m3/day (80,000 BWPD), with a turndown capacity to 8,745 m3/day (55,000 BWPD).
Project Scope:
The project scope consists of a single process module comprising Coarse filters, UF Multi Media Element Vessel, SRP Feed pumps, SRP Train, Deaerator Tower and Vacuum package, Water Injection Booster Pumps, Water Injection Pump and Chemical Injection package
Process Description:
The system has been designed to produce 80,000 bwpd of Water for Injection.
Prior to entering the Ultrafiltration system, the seawater passes through 1 duty (1 standby) Coarse Strainers. This filtrate is then directed to the Ultrafiltration system feed.
In normal operation the UF trains process sufficient water for the downstream SRP, with the number of trains online providing the signal for more or less water to be delivered.
Each of the MEV trains is equipped with a feed control valve whose signal and subsequent position is provided by feedback from the control system as to how many SRP trains are online. A call for more filtrate will result in the feed control valves opening to allow more filtrate to be produced and vice versa.
The UF package always maintains a constant filtrate capacity irrespective of the number of trains online assuming normal operation. Over any typical 24 hour period, the package will normally operate between N+2, SASFF (simultaneous air scour and forward flush), and SASFF+CEB (Chemically Enhanced Backwash). This indicates a stable operational envelope that is unlikely to experience excessive CIP frequency. With one train offline for a prolonged period, we would recommend altering the package control system to prevent simultaneous CEB and SASFF in order to limit high instantaneous flux rates. From the UF the filtrate is feed to the Vacuum Deaerator Package.
The Seawater is routed to the suction of the SRU Pumps in a 4 x 25% configuration. To protect the minimum flow characteristics of the SRU HP feed pumps, the pump discharges are provided with a minimum flow valve. Downstream of the pumps scale inhibitor is dosed for precipitation control and a non-oxidising biocide is dosed intermittently for biological control of the membranes.
2 x 50% SRU trains treats the feed stream in a two stage operation. The feed pressure to each SRU is controlled based on the permeate flow set point. The 1st pass SRU train produces 75% of the feed flow as low sulphate permeate. The remaining 25% of the feed flow ends up as high sulphate content reject Seawater and is directed to the plant drain system.
The low sulphate SW from each SRU is merged and then directed to the Deaerator.
The Vacuum Deaerator Package is comprised of a single two-stage vacuum deaeration tower and the Vacuum Package. The filtered feed stream is evenly distributed over the internal diameter of the deaeration tower where the water flow is allowed to free-fall over the packing. This serves to create a high liquid thin film surface area thus allowing the entrained gases, specifically oxygen, to exit the water prior to entering the integral retention basin of the deaeration tower. In order to protect the downstream membrane system from an oxidizing environment, sodium bisulphite is dosed in to the deaeration tower’s retention basin. The addition of sodium bisulphite reduces the residual chlorine and has the added benefit of scavenging the remaining oxygen in the seawater. A minimum working retention volume of two (2) minutes from low level has been provided.
There also is a common membrane cleaning in place (CIP) skid for the SRP and UF trains.