Client: MODEC
Process: Sulphate Removal
Country: Tartaruga Verde and Tartaruga Mestiça fields, Campos Basin, Offshore Brazil.
Contract Description: Supply of Sulphate Removal
Contract Date: April 2015
Contract Completion Date: May 2016
Plant Capacity: 237,232 BPD / 37,720 m3/day
Sea Water Conversion: 75%
Sea Water Feed Quality
- TDS: 35,685
- Sulphate: 2,400 mg/l
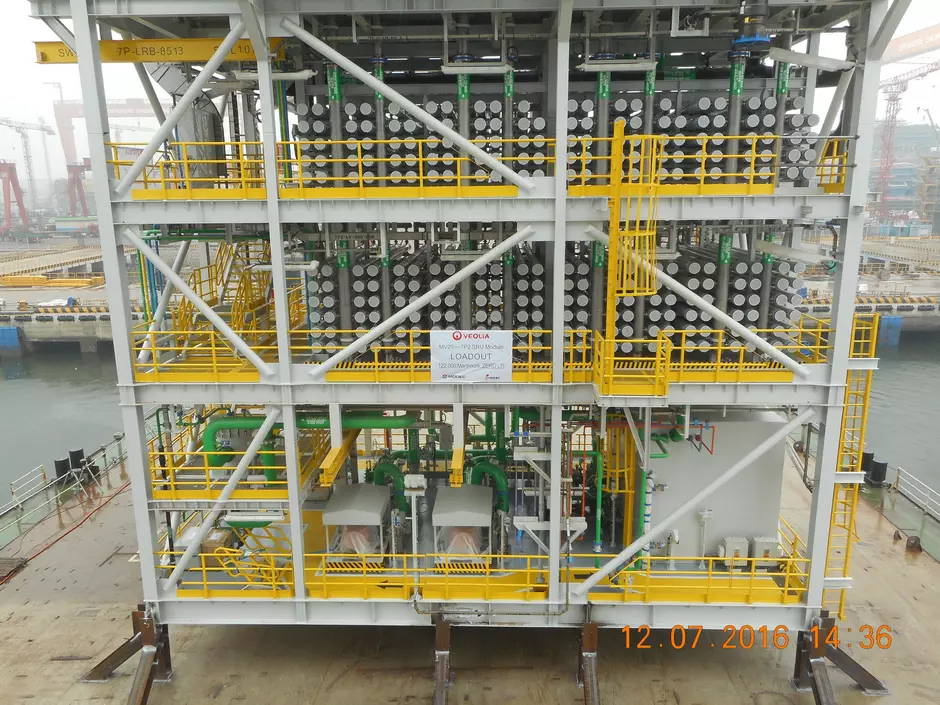
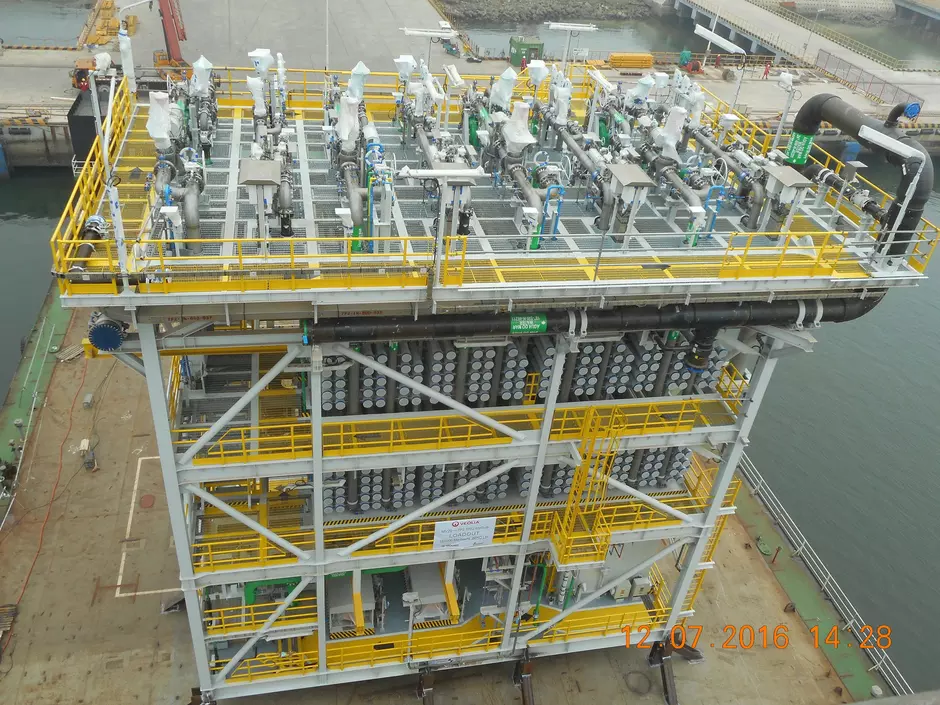
Project Description:
The project is for the complete seawater treatment package skids for the Seawater Treatment Module for production of low Sulphate Seawater for injection into the reservoir for the MV29 (Tupi 10) FPSO project located in the Tartaruga Verde and Tartaruga Mestiça fields in the Campos Basin Brazil. The plant consists of pre-treatment equipment, a sulphate removal package skid and a standalone deaerator vessel – all equipment to be installed by others onto a pancake, also provided by others.
Project Scope:
The scope consists of a Seawater Treatment Plant in a multi-skid arrangement comprising: Seawater Coarse Strainers, Multi Media Fine Filtration, Upstream Vacuum Deaerator Package, Sulphate Removal Feed Pumps, Cartridge Filters, Sulphate Removal Membrane System, Clean In Place System, Piping, Valves and Instrumentation.
Process Description:
Seawater is pumped using the Seawater Lift Pumps (provided by others) and directed to the seawater treatment system. The raw seawater is chlorinated via the electrochlorination package (by others) and introduced into the seawater lift pump suction lines. Sodium hypochlorite is used to limit the potential of biological activity in the downstream processes.
2 x 100% manual clean seawater coarse filters remove particulate matter from the feed stream to the SRP coarse strainers and other consumers nominally down to 1000 microns.
2 x 100% automatic backwashable SRP coarse filters remove particulate matter from the feed stream to the SRP plant nominally down to 80 microns (98% removal).
Coarse filtered water is routed to the Multi-Media Filters that remove the majority of particulates 3 microns or greater.
The fine filtered seawater is routed to the suction of the Sulphate Removal Unit Feed Pumps to boost the conditioned water to the required feed pressure for the membranes. The three SR Feed Pumps (2 duty & 1 spare) operate in parallel. Antiscalant is dosed into the common suction piping of the Sulphate Removal Feed Pumps, decreasing the scaling tendency by limiting the formation of sparingly soluble salts in the membrane system. A non-oxidizing proprietary biocide for treating the SR90 membranes is also periodically batch dosed into the common suction piping of the Sulphate Removal Feed Pumps. Finally, SBS is also dosed into the common suction piping of the Sulphate Removal Feed Pumps to remove the residual chlorine present in the seawater to prevent irreparable damage to the SR90 membranes.
Parallel operating Cartridge Filters (2 duty & 1 spare), each containing 10-micron (absolute) replaceable polypropylene elements provide the final required particulate filtration prior the SR membranes.
The seawater flows to parallel operated Sulphate Removal Units .
The feed pressure to each SRU is controlled based on the permeate flow set point. The SRU produces 75% of the feed flow as low sulphate permeate Seawater. The low sulphate SW from each SRU is merged and then directed to the cooling medium heat exchanger prior to the water injection pumps. The remaining 25% of the feed flow ends up as high sulphate content reject seawater and is directed overboard.
The fine filtered water then enters the Vacuum Deaerator to remove dissolved oxygen from the water. Oxygen scavenger is dosed to the sump of the deaerator to chemically reduce the remaining oxygen to levels of 10ppb or less.
Deaerated, low sulphate injection water from the deaerator is routed to 3 x 50% water injection booster pumps . These pumps are provided to boost the feed pressure to the downstream water injection pumps via the cooling water heat exchangers (all provided by others) to 8.5 barg.
There also is a membrane cleaning in Place (CIP) system for the SR trains. The CIP system is designed to clean either one or two trains of membranes at a time.