Sulphate Removal Process (SRP)
The Sulphate Removal Process (SRP) extracts the sulphates from seawater prior to injection into the oil bearing reservoir, this is seen as the most economical way to prevent scaling that would form if untreated water met barium or strontium that's present in formation water. Other salts (sodium, chloride etc.) are substantially unaffected, thus maintaining the stability and permeability of the formation clays.
BENEFITS OF SULPHATE REMOVAL
Prevents well souring by controlling sulphate reducing bacteria (SRB)
Assists in maintaining reservoir permeability by limiting formation plugging caused by scaling
Eliminates economic and operational impacts resulting from scaling in reservoir
Significantly reduces sulphate scale precipitation in production wells
Each SRP system is bespoke, designed to our clients specific requirements and combines the below technologies.
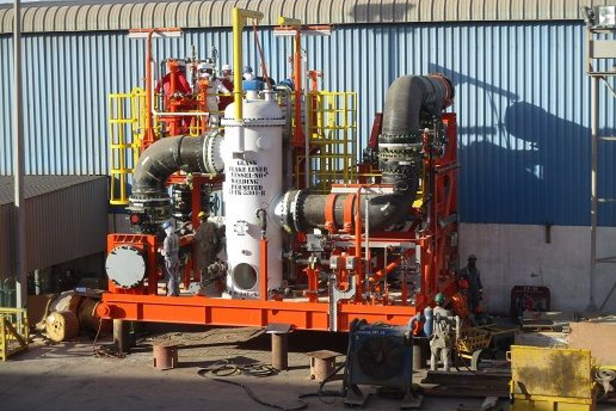
The objective of this process is to remove coarse suspended solids that could deposit on process equipment creating scale and corrosion site.
The UltraMEV combines multiple ultrafiltration elements in a single housing reducing footprint, weight and need for interconnecting pipework.
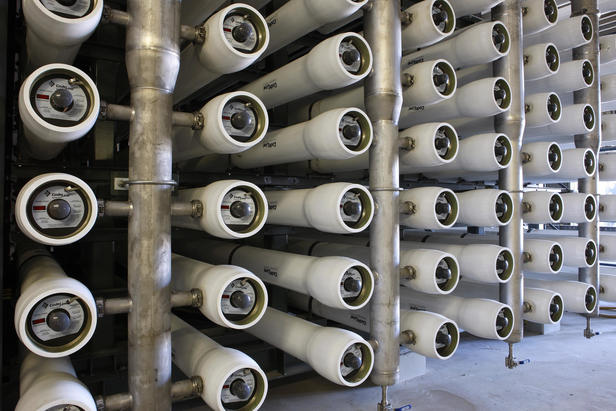
The nanofiltration membranes are specifically designed to remove sulphate ions from seawater used for water injection and sea water reverse osmosis
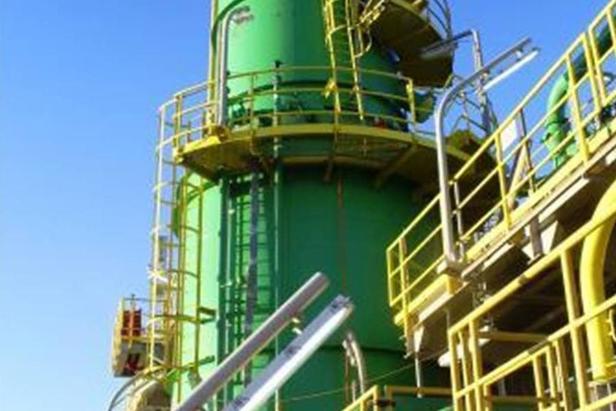
A deaerator removes oxygen and other dissolved gases from water, such as feedwater and is designed to receive a chemically treated and filtered flow stream.
The Multi Media filtration system works on depth filtration principles to treat the SRP / SWRO feed water to remove the majority of particles.
Generally installed downstream of the multimedia filters to perform a guard function ahead of the SR or RO membrane stage
Where oilfield reservoir formation water contains significant amounts of barium and/or strontium, injection of seawater can cause barium and strontium sulphate scale to be formed. These scales have the effect of reducing reservoir permeability and can also become deposited in production pipe internals. Barium and strontium sulphate scales are notoriously difficult to remove since they cannot be easily dissolved. Squeeze inhibition treatments are often utilised to improve the well permeability but these are extremely difficult to control and cannot be applied to complex sub-sea networks or from floating production storage and off-loading vessels (FPSO). Where pipeline scaling is experienced, this has to be removed by mechanical means.
As an alternative to the removal of scale by mechanical means, the installation of a Sulphate Removal Plant (SRP), to extract the sulphates from the seawater prior to injection, is often seen as the most economical approach. The SRP uses nano-filtration membranes to remove the sulphates while leaving the other salts (sodium, chloride etc.) substantially unaffected, thus maintaining the stability and permeability of the formation clays.
This process was invented in the late 1980's by The Marathon Oil Company, using Dow Chemical's membranes.
The membranes are typically configured in a SRP with a "2-array, brine staged" arrangement. With this arrangement, the seawater feed is introduced to the first array of membranes which allows 50% of the feed to pass through the membrane material with the sulphate being rejected on the membrane surface. The 50% reject water (or brine) is then fed to the second array of membranes where again 50% passes through as low sulphate water. The two flows of low sulphate water are blended to give an overall recovery of 75% with the remaining 25% of increased sulphate reject being safely discharged overboard without endangering the environment.